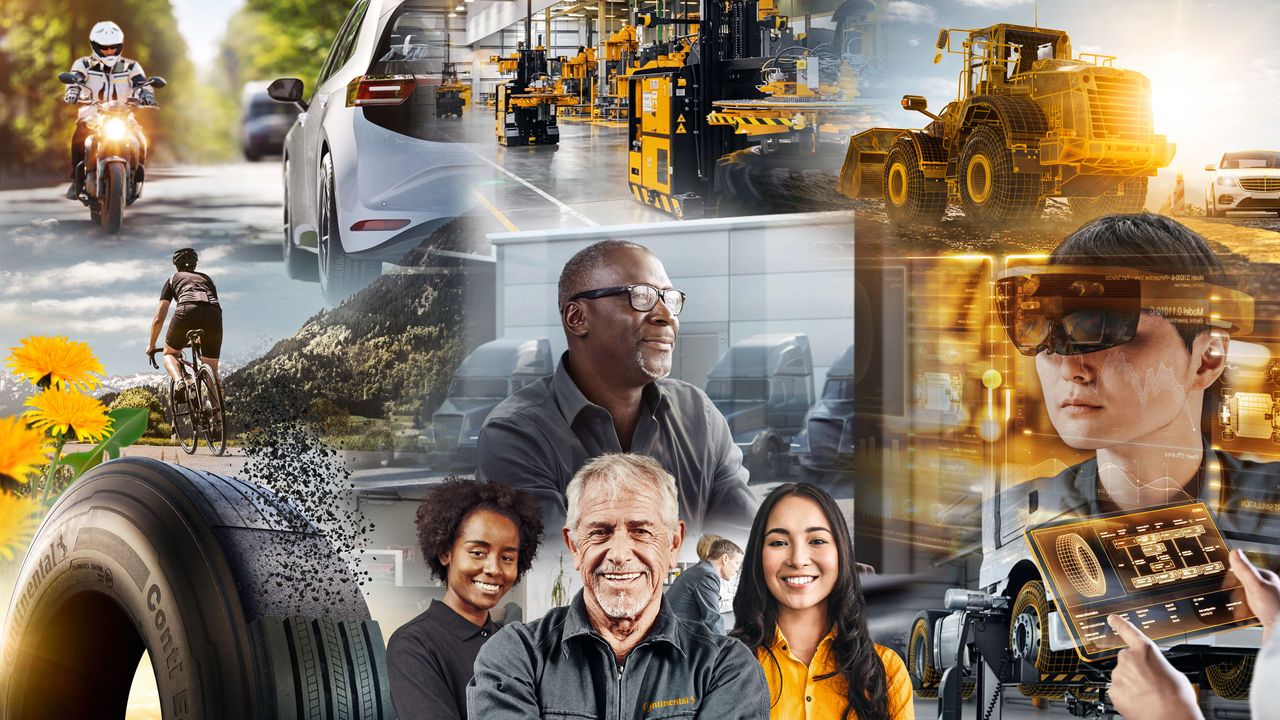
Rubber tires have been manufactured for over 100 years. We have been heavily involved in their development.
Today, a modern car tire consists of 25 components and 12 different rubber compounds on average. We exclusively use materials of the highest quality and set high standards – especially in terms of safety.
High-quality raw materials are turned into a tire in five steps:
A large proportion of the tire consists of natural and synthetic rubber. Natural rubber is obtained almost exclusively from the rubber tree. Once it has coagulated, the clumps are cleaned with water and pressed into firm balls that are in turn mixed with other additives according to a precise formula. Synthetic rubber is made from a mixture of different additives in a laboratory using an artificial process. Generally, rubber offers a high degree of skid resistance and, depending on its processing, the desired elasticity. For a modern car tire, we use up to 12 different rubber compounds.
Numerous additives, including synthetic rubber as well as carbon black and silica, are used to improve resistance to wear and aging as well as the grip of a tire. High tensile steel, which is needed for making the steel belt (steel cord) as well as the wire core (steel wire), is used as a source material. Textiles such as rayon, nylon, polyester, and aramid fibers, are used in the manufacturing of the cord and strengthen the tire.
The composite materials are combined to make constituent parts of a tire. The rubber and the pre-treated steel cords that are delivered on wire reels are fed into a calender. The steel cords are encased in one layer or multiple layers of rubber. This produces a long, continuous sheet of cord and rubber that is cut to the correct length at a certain angle depending on the tire size and then rolled up for further processing.
For the tread that forms the connection to the road and the sidewall, kneadable rubber material that has been made in a mixing plant is made into a long, continuous strip by a screw-type extruder. After the extrusion process, the weight per meter is checked and the tread is cooled in an immersion bath. The tread strip is then cut to the correct length for the tire size, at which point a further unit weight check is carried out. The extruder also makes sidewall sections that are cut to suit the tire size.
The textile threads are fed into the calender where they are embedded in a thin layer of rubber. This long, continuous sheet is cut to the desired width at a 90° angle to the threads’ direction of travel and wound up for further processing. It forms the textile cord ply that holds the internal pressure and keeps the tire in the correct shape.
The air-tight inner liner is made into a wide, thin layer by a calender. This component seals the air-filled inner chamber and regulates the tire pressure. In modern tubeless tires, the inner liner replaces the tube.
The bead core is the connection between the tire and the rim and consists of many ring-shaped steel wires, each of which has its own rubber coating. We subsequently fit this ring with a rubber profile.
Once all the components have been made, tire assembly can begin. All components are joined together to form a green tire with the aid of the tire building machine. This is done in two stages: the carcass first and then the tread/belt. We spray the green tire with a special fluid to prepare it for vulcanization.
The curing process: the tire takes on its final shape after being vulcanized at a certain pressure and temperature for a certain time. Vulcanization turns the crude rubber into flexible, elastic rubber. The tire is also given its tread pattern and sidewall markings in the vulcanization press molds.
We use a multi-stage process to ensure that the finished tires meet our exacting quality requirements. Each individual step in production – from the inspection of the raw materials to the delivery of the tire – is subject to ongoing quality control. In the last step, we check our finished tires using three procedures:
We pass our tires onto the distribution warehouse only once they have passed all checks and inspections.