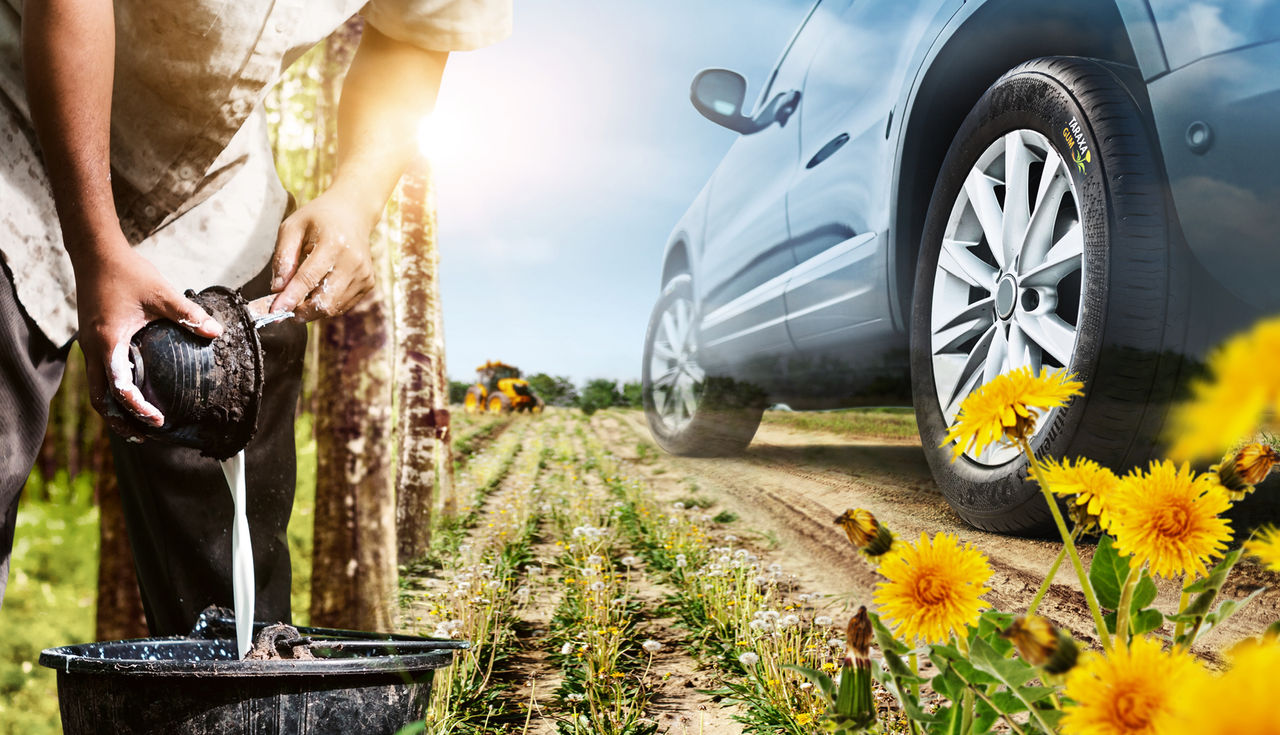
Continental Tires continuously analyzes and reviews the raw materials used in tire production. For example, the more environmentally friendly COKOON bonding technology allows textile reinforcements to be bonded to rubber compounds without the use of resorcinol or formaldehyde in the textile dip bath. This is a key application in the rubber industry, as textile reinforcements are widely used in tire production as well as in the manufacture of technical rubber products such as hoses and conveyor belts. Continental and Kordsa, a global supplier of textile reinforcing materials, have made COKOON available to all tire manufacturers and their suppliers as a royalty-free, open-source solution.
For about a century, the resorcinol-formaldehyde latex dipping process has been the most widely used technology for bonding textile fibers to rubber. This process is used not only in tire manufacturing, but also in the production of other rubber products. Both formaldehyde and resorcinol have certain properties that lead us to limit their use as much as possible. At Continental, we are committed to safer and more sustainable practices, not only in our own production, but throughout the industry. Both formaldehyde and resorcinol are used early in the production chain and are chemically modified by the conversion process, so they pose no risk to our employees in tire plants and end-consumers. However, we believe it is our responsibility to avoid these substances wherever possible. By switching to alternative bonding systems, we aim to create a safer and more sustainable industry. This proactive approach is not only in line with our commitment to sustainability, but also allows us to set a new standard for the industry through our open source approach.
Developing a technology like COKOON requires a lot of motivation, patience and perseverance. The viability and development of our company depends in particular on the close cooperation of our global team and on working for one another. We stand united, combining forces across the organization and putting aside individual interests. In this way, we achieve the greatest possible value and success for Continental. This culture is evident in our daily work and in our collaboration with our partner Kordsa, where our efficient and effective cooperation is highly valued.
In addition, the sustainability aspect of COKOON technology is an important motivation for us. The development of COKOON aims to eliminate resorcinol and formaldehyde from tire production, contributing to a safer and more sustainable industry.
Open innovation approaches aim to simplify processes and bring companies together for a common goal.
Open source models like COKOON require a new way of thinking. Normally, innovation is the key to differentiation. However, to replace resorcinol formaldehyde latex technology, we at Continental, together with Kordsa, believe that an open source approach is the best way to overcome the challenges of competing single source solutions. Single-source solutions often complicate the market by requiring us to compare and manage different adhesive systems. Each requires separate cost and time demanding approval and testing. By introducing an open-source model managed by the independent law firm AdvInno, we want to avoid single source solutions and promote collaboration.
It was particularly challenging to compete with the established Resorcinol Formaldehyde Latex (RFL) dipping technology, which has been optimized for decades for various textiles and applications in tires and other rubber goods. Together with Kordsa, we have developed a universal solution that maintains the high performance level, uses widely available materials to avoid single-sourcing, and can be integrated into standard production processes.
More sustainable materials are becoming increasingly important and have evolved from a "nice to have" to an important priority in industry. At Continental, we are working intensively to replace as many raw materials as possible with more sustainable alternatives in production, while maintaining our high quality standards. By 2030, we aim to use more than 40 percent renewable and recycled materials in our tires.
From the introduction of the UltraContact NXT, our most sustainable production tire on the market, to the progress we are making in decarbonizing our sites, we are proud to be at the leading edge of this development, constantly pushing the boundaries to create more sustainable solutions for the future of mobility.