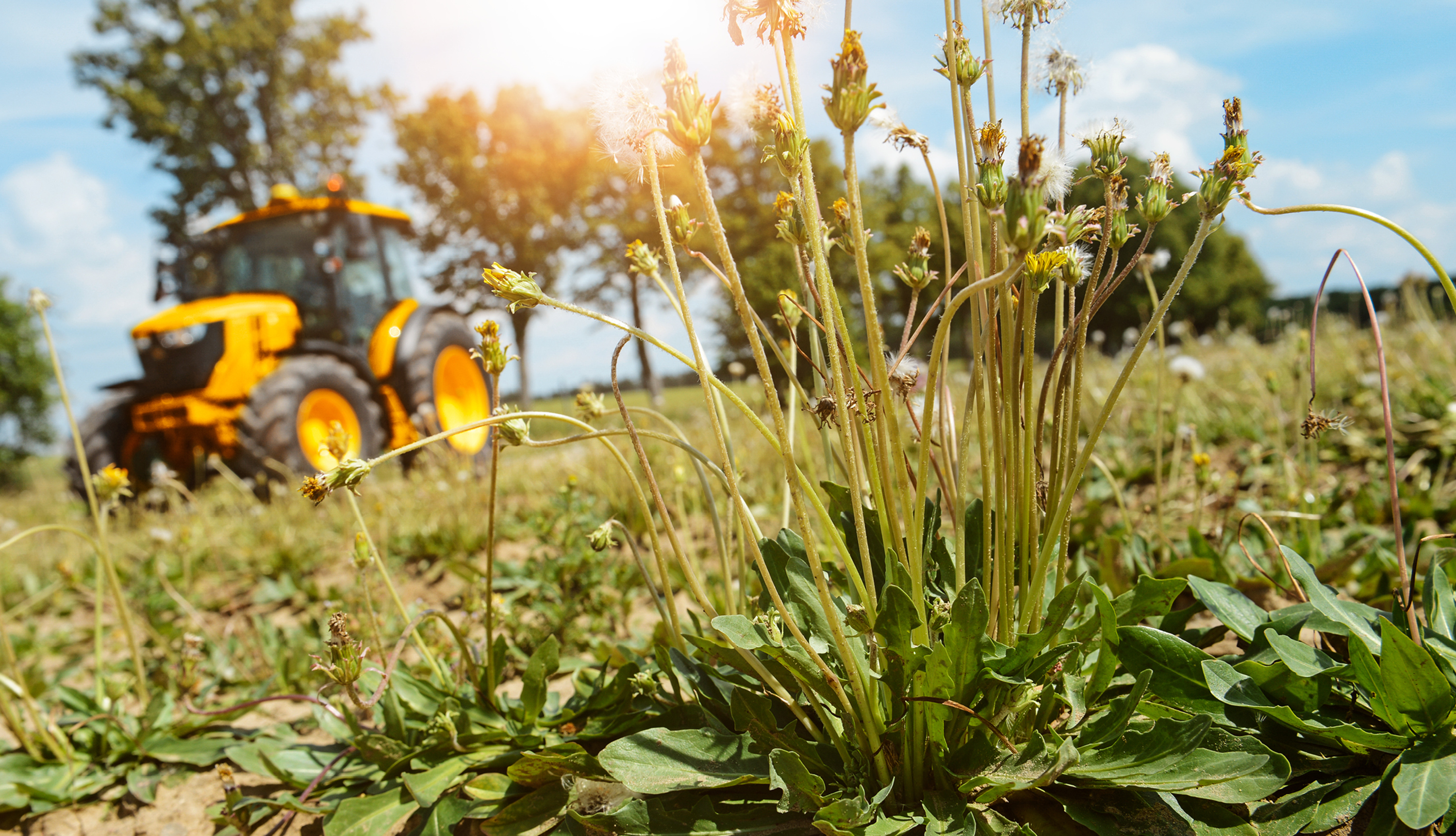
We believe that circular economy is the model of the future. Our ambition is to increase the use of sustainable materials in our tire products to 100 percent by 2050 at the latest. Recycled materials are expected to make a significant contribution to this. By 2050 at the latest, we want to use 60 percent of materials recovered from end-of-life tires in tire construction.
As part of a closed-loop system, tires will in future become the raw material for new tires.
Jorge Almeida, Head of Sustainability Continental Tires
Tires are made from a variety of materials and must meet the highest safety requirements. What is already common practice for plastics, glass, paper and many metals is a challenge for tires: producing new tires from old ones.
Tires consist of different components and rubber compounds. Some components, such as steel, but also the tread, can already be separated from each other by mechanical recycling. With rubber compounds, this is more difficult and requires intermediate chemical steps.
The challenges involved can be well illustrated using plasticine:
Tires consist of a carcass and a tread. While the carcass is often still intact, the tread has already reached the end of its service life. During retreading, the tread is removed and replaced, as is the sidewall of the tire during one of the retreading processes, called hot retreading. The carcass is thus prepared for a second and even third tire life. We use state-of-the-art analysis processes, production methods and recycling technologies.
We have been setting an example for sustainability with the retreading of truck tires since 1903. By extending the service life of tires, we have been helping to conserve resources and reduce costs for over 120 years. Every year, we retread more than one million truck and bus tires worldwide. According to a study by the Fraunhofer Institute for Environmental, Safety and Energy Technology (UMSICHT), retreaded tires reduce CO2 emissions by up to 50 percent compared to new tires. They also consist of up to 85 percent recycled and renewable materials. In terms of traction, grip and safety, they offer performance comparable to new tires.
In 2013, we opened our ContiLifeCycle plant in Hanover-Stöcken, which combines a retreading and recycling plant. With an integrated approach of hot retreading and a specially developed rubber recycling plant, we are actively committed to the sustainable use of raw materials, water and energy. Since the plant was set up, around 10,000 tons of material have gone into new compounds that would have become waste without the recycling process. The ContiLifeCycle plant has thus been making a contribution to greater sustainability in the tire industry since its commissioning.
As part of pyrolysis, rubber compounds can be separated into some of their starting materials. This applies above all to oil, gas and carbon. Pyrolysis oil, for example, can be used to produce new raw materials. In order to further optimize the recycling of end-of-life tires by pyrolysis, Continental is collaborating with Pyrum Innovations, among others.
Pyrum decomposes Continental's end-of-life tires into individual components in industrial furnaces using a special pyrolysis process. In this way, valuable raw materials contained in end-of-life tires can be extracted and recycled. Both companies are working towards obtaining high-quality carbon black and high-quality raw materials from the pyrolysis oil obtained for Continental's tire production in the medium term. Recycled carbon black is already used in all forklift tires manufactured at Continental's tire plant in Korbach, Germany. In the next step, recycled carbon black is to be used in passenger car tires.
In the long term, both companies are striving for a closed circular economy concept for the recycling of end-of-life tires.
The material complexity of a tire makes recycling more complicated compared to products made from one or a few types of material.
Tire recycling requires advanced technologies and processes, which Continental is driving forward together with partners. The aim is to develop recycled materials whose performance is on a par with conventional raw materials. After all, the quality of tires has a significant influence on the handling and stability of a vehicle. Safety is a top priority for Continental.
We are the only selected tire manufacturer to contribute our extensive expertise to the EU ZEvRA project!
The aim of the project is to show how the circularity of electric vehicles can be improved along the entire value chain - in line with the European Union's goal of achieving zero CO2e emissions by 2035.
We are using our extensive know-how and working on a concept tire that uses as much recycled material as possible.