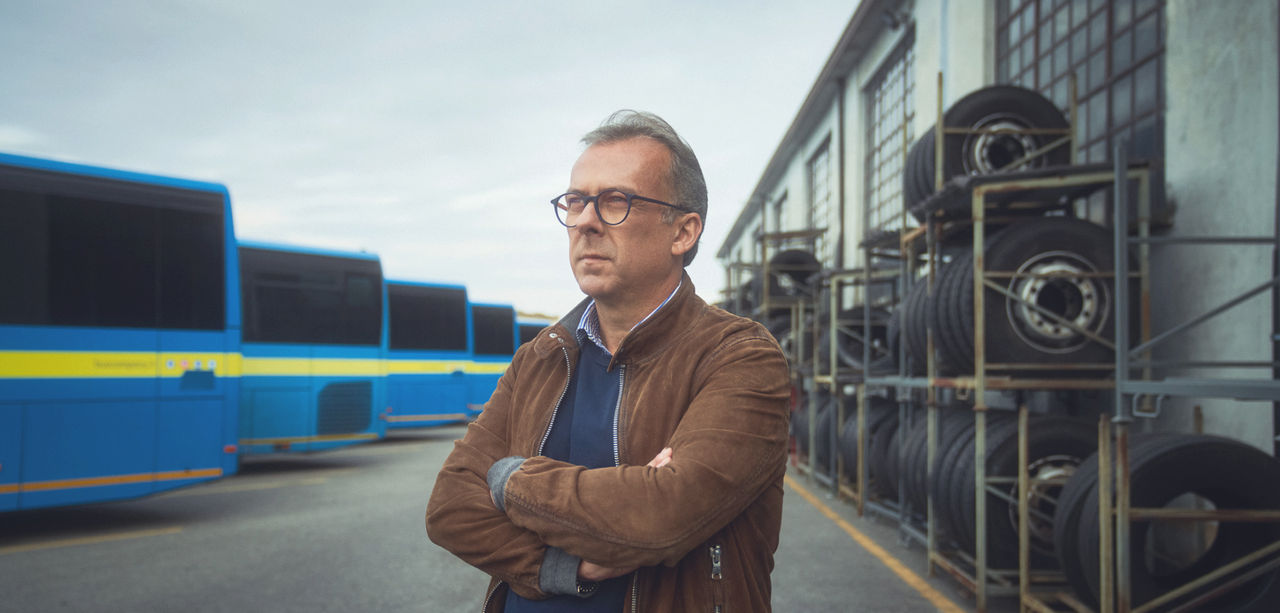
There is a constant price war at play in the transportation industry. Using digital technologies to save on costs can be the key to success.” explains Andy Baum, Managing Director of Klaus Baum Logistik from Eupen in Belgium. Baum joined his father’s company more than a decade ago. Since then, he has done a lot to make the fleet fit for the future. One step was the investment in ContiConnect Live. The tire management solution provides real-time tire data around the clock, regardless of the location of the vehicles. If a problem occurs, Baum is informed by a push notification and can send his own repair vehicle or arrange an appointment with a repair shop. For him, this is a real innovation for the transport efficiency and fleet safety of the family business.
There is a constant price war at play in the transportation industry. Using digital technologies to save on costs can be the key to success
Andy Baum, Managing Director of Klaus Baum Logistik.
Eupen, Belgium
The haulage company’s trucks move more than 4,000 tons of freight per week and cover an average distance of 2,650 kilometers. Since the vehicles are on the road from Monday to Friday, the tires can only be serviced manually at the weekend. This stress will be eliminated thanks to ContiConnect, at least when all 43 vehicles are equipped with the sensors. "My aim is to make my fleet more reliable. Checking tire pressure, no more punctures, and more safety for our 55 drivers – for me, these are the three most important benefits of ContiConnect Live,” summarizes Baum.
The fleet primarily transports steel products for the automotive industry from the port of Antwerp, the second largest in Europe, to Germany. Punctual delivery of goods according to the just-in-time principle is essential. If Baum receives a push notification from the ContiConnect app, he reacts immediately. He has learned that he can rely on the system one hundred percent. For example, when the app reported a loss of pressure in a tire a few months ago. This had not yet been noticed by the driver. The closest workshop in the vicinity discovered a small puncture in the tire. After an hour, the tire was repaired and the vehicle was back on the road.
But the haulage company’s history did not begin in the digital present. In 1984, the then 23-year-old truck driver Klaus Baum, Andy Baum’s father, bought his first vehicle. He built up the company with a great deal of personal commitment. He had a small warehouse built behind the family home. The vehicle fleet now delivers goods to Luxembourg, Germany, the Netherlands, and Belgium. Eupen is home to an impressive logistics center with its own workshop, wash facility, and 2,300 square meters of storage space. The small hall that Klaus Baum built back then stands next to it and acts like a signpost – this is where we come from, this is where we are going. Klaus Baum no longer drives his own routes, but whenever the need arises, he gets on a forklift truck and helps with the loading of goods.
The company’s success is also down to the excellent teamwork between father and son. Andy Baum joined the haulage company back in 2012. Today, he steers the course of the family business from his new office in Luxembourg, with a clear vision: “My aim is to continue to run the company just as my father would – with a combination of tradition and fresh ideas.” There is hardly any friction between the two. “Ultimately, we must always act in the interests of the company. Personal vanity plays no role for us,” says Andy Baum. He commutes to Luxembourg four days a week together with three co-workers. They spend two hours in the car talking about the job, the day ahead, family. In Luxembourg, Baum sits in the middle of the open-plan office, surrounded by his employees. Meetings are held in an informal manner. “We all work side by side, that’s part of our company philosophy. I think our people really appreciate that,” says Andy Baum. He uses his weekly day in Eupen to discuss ideas with his co-workers on site and for the scheduling of vehicles from Belgium to Germany. He doesn’t have a regular working day: “I love the flexibility! I am in contact with a lot of people, be it the drivers or our customers. Making a contribution to society, transporting goods from A to B and making sure that the food is on the shelves – that’s what drives me every day.”
When Baum is not working, he spends time with his family in Eupen. His son is two and a half years old. To ensure that the next generation of Baums – if they so wish – are able to continue to run the business, the fleet is to be made more efficient, safer, and more reliable using digital technologies. Andy Baum explains: “The key for us is to digitize as many processes as possible. By 2025, we want to be entirely paperless. In future, our drivers will receive ContiConnect data on their smartphones and our customers will be able to track their goods via GPS. Bills of lading will then be sent directly a few hours after the goods have been unloaded. This saves time, costs, and is transparent.”
Baum would like Continental to provide tire management software, including for tracking tire tread depth and carrying out tire inventory management, so that the performance of each individual tire can be evaluated. Looking to the future of the logistics industry, he speculates: “I think electric or hydrogen-powered trucks will be the next big trend, as well as driverless vans. But that will probably take some time.” Until then, Andy Baum will continue to focus on digital tire management and truck fleet optimization. For the haulage company and its customers.
Get in touch for a custom consultation