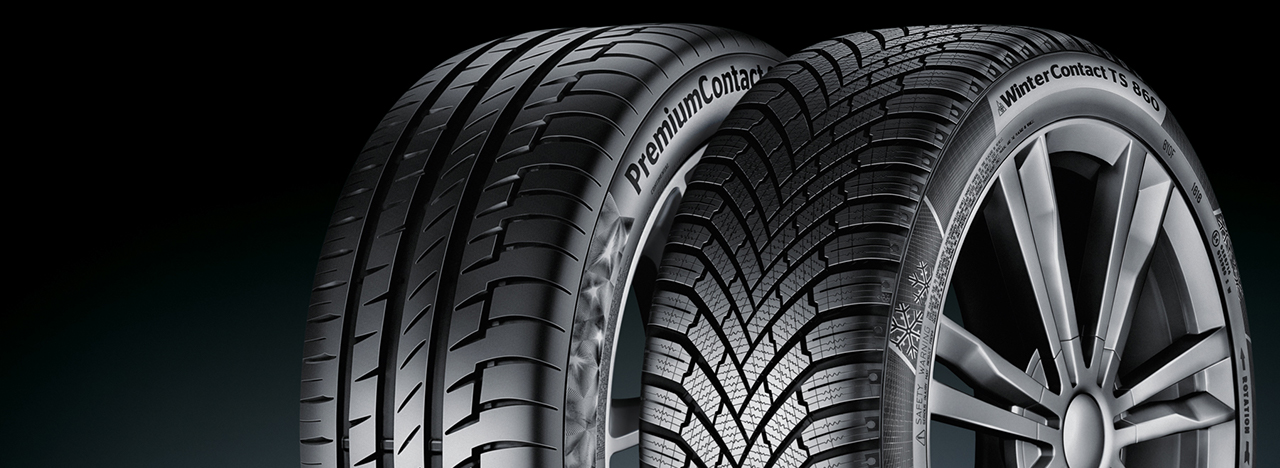
Modern passenger car tires have a complex structure. The rubber tires we drive on today have been in the making for over a century. Continental has played a major role in the development of today’s steel-belted radial tires, improving tire design and function. Read on to discover how as we dissect the modern tire.
Tire components can be grouped into two main structural elements: The tread and belt assembly and the casing. These elements consist of several layers.
Starting at the road surface and working our way to the core of the tire, let’s take a look at the individual components. We’ll also discover what role these components play.
Let’s start with the outer layers that make up the tread and belt of the tire. This principally rubber component envelops the casing and provides low rolling resistance, optimum handling, a long life and good gas mileage.
1. Tread Pattern. The tread establishes the connection to the road and consits of a special rubber compound and the individual tire pattern. The tire tread has three areas:
Continental’s contribution. In 1904, Continental was the first tire manufacturer to introduce a tread pattern to the pneumatic tires of the time.
2. Winding bandage. Directly unter the tread is the winding bandage. It consists of nylon threads embedded in rubber. It improves driving characteristics at high speeds. Imagine gathering a length of twine back into a ball, coiling it around and around. The winding bandage is a little like this. They consist of a single, strong cord of nylon, embedded in rubber. This cord spirals around the circumference of the tire, from one side to the other, without overlapping.
Continental’s contribution. A woven linen fabric embedded in rubber used to perform this function. But the crossed threads would rub against each other, resulting in a shorter tire life. In 1923, Continental introduced a new cord fabric. This fabric (described above) featured cords running in one direction held in place by supporting threads, embedded in rubber. Tires incorporating the new fabric lasted much longer.
3. Steel cord belt. High-strength steel wires (cords) form the next layer, the steel cord belt layer. They give the tire shape and strength, optimize rolling resistance and mileage.
Now let’s discover the interior of the tire, known as the casing or carcass. The casing cushions the tire and contains air – functioning like an inner tube. It’s the air – not the tire itself – that carries the load. That's why inflation pressure is so important. Anyone who has ever had a flat tire knows this well!
4. Textile carcass. The load-bearing framework of the tire, the carcass, consists of a textile fabric based on rubberized fibers. This textile carcass regulates the internal pressure together with the inner layer.
5. Inner layer. The inner layer ensures airtightness and is made of synthetic rubber.
Part of the casing, the tire bead component makes up the edge of the tire that sits securely on the wheel groove. It’s here that the tire is held in place on the wheel thanks to air pressure. The bead is made up of three parts.
7. Tire bead, 8. Core profile, 9. Steel core
The steel core and the core profile form the tire bead. This ensures tire seating on the rim, safe handling and driving comfort.
Read more here about how these components come together in the tire-building process.