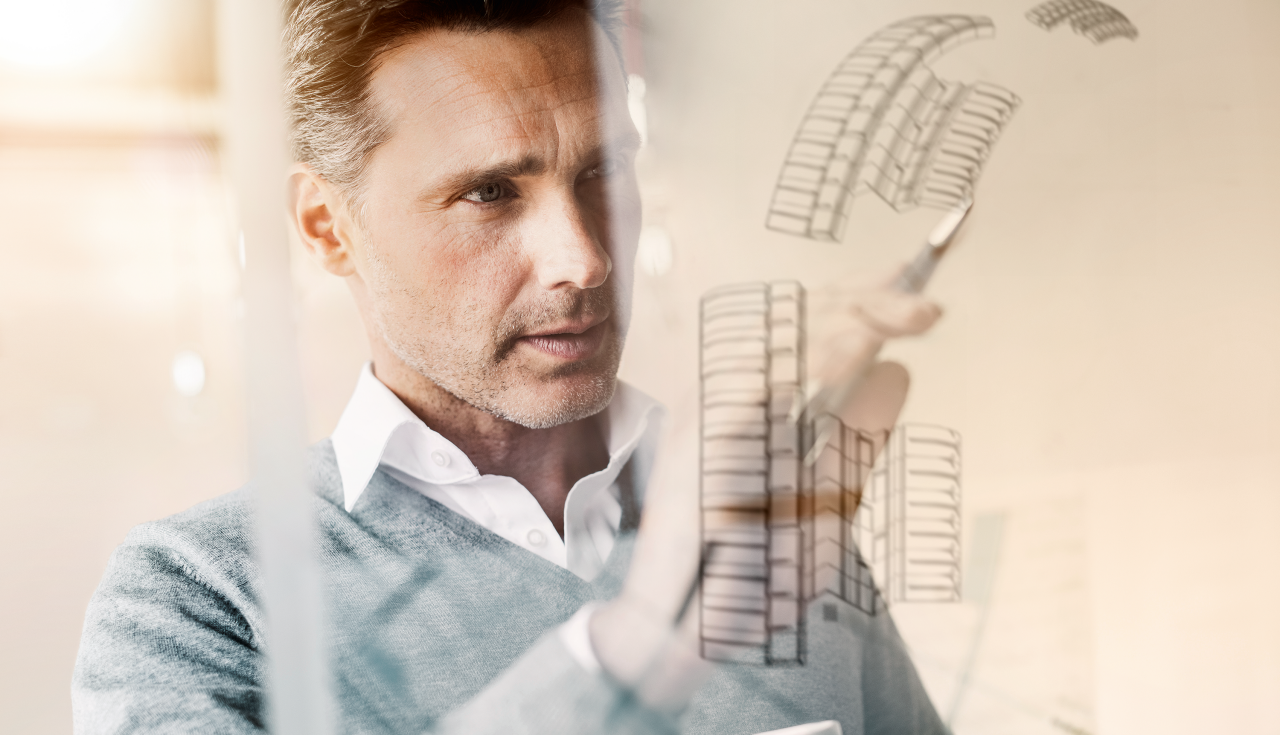
Construction of an in-house, state-of-the-art laboratory for research of applied rubber chemistry at the Hanover Vahrenwald plant.
Construction
Tread
Materials
All three areas have a direct impact on the performance, safety and service life of a tire. That's why our engineers are constantly developing them and constantly pushing physical boundaries.
As early as 1898, Continental began manufacturing pneumatic tires for cars. Visually, there are few differences between modern tires and those of decades ago. But technology, materials and manufacturing processes have changed significantly since then.
Construction of an in-house, state-of-the-art laboratory for research of applied rubber chemistry at the Hanover Vahrenwald plant.
The free-running bicycle with coaster brake enjoys worldwide popularity. Continental is the first German company to manufacture pneumatic bicycle tires.
Continental relies on the use of synthetic rubber for the first time.
On the occasion of its 50th anniversary in 1921, Continental was the first German company to launch giant tires for commercial vehicles.
In addition, from this year onwards, finely woven cords replace the less supple linen fabric in the hoops. This increases comfort and reduces heat generation and fuel consumption.
Continental tires turn black. The use of carbon black not only changes the color of the tire, but also has a positive effect on the stability, strength and durability of tires.
Continental builds Europe's first pneumatic agricultural tire. The tire design is adapted to the requirements of the tire. For the first time, it is possible to drive safely with tractors both on the road and in the field.
Continental applies for a patent for the tubeless tire.
An invention whose basic technological principle is still used today.
Continental develops the first radial tire. It offers more grip, better steering characteristics, greater driving comfort and a long service life. And thus contributes to greater safety in road traffic.
The first steel-reinforced tire rolls off the production line and is marketed under the name "TS 771", where "TS" stands for "textile steel".
Continental is launching the first winter tire on the market that can boast a truly winter-proof tread compound. Previously, only constructive elements such as spikes were used.
Continental is launching a large-scale research and development project under the keyword EOT (Energy Optimized Tyre), which will result in a tire with 25 percent lower rolling resistance and a 30 percent increase in mileage. This project is the starting point for the development of modern fuel-saving tires and culminates in the presentation of the ContiEcoContact for passenger cars in 1992 and the presentation of the Conti-EcoPlus tire line for commercial vehicles in 2012.
The tire manufacturer is using silica as a filler in its tires for the first time, presenting the first tire designed specifically for energy efficiency and lower energy consumption: the ContiEcoContact CP. The use of silica significantly optimizes the tire properties and makes the tire line a great success product.
The ContiSeal technology was introduced. A viscous adhesive layer in the tire seals damage with a diameter of up to 5 millimeters.
The ContiSilent technology reduces driving noise inside the car. A special layer of polyurethane foam on the inside of the tire tread dampens the cavity noise inside the tire and prevents it from being transmitted through the body.
With up to 65% sustainable materials, our UltraContact NXT is the most sustainable production tire on the market.
The carcass is an important reinforcing element of the tire. The fabric layers within the carcasses can be arranged in different ways: in the so-called cross-ply pattern or in a radial design.
Until 1960, the carcass initially consisted of several layers of fabric, which were arranged on top of each other at a relatively large angle, and ran diagonally to the direction of rotation. This cross-structured layout brought the name of the early pneumatic tires, also known as "cross-ply tires."
Cross-ply tires already had greatly improved shock-absorbing properties.
In contrast to cross-ply tires, the carcass fibers of a radial tire are arranged exactly at right angles (90 degrees) to the direction of travel.
This type of arrangement was developed as early as 1946 and has dominated since the early 1960s.
Radial tires allow for better absorption of shocks on the road, allowing them to convert the car's performance more efficiently. Due to their design, radial tires provide better contact with the road surface, which simplifies steering and provides greater driving comfort. Even on wet roads or corners, radial tires offer a high level of control. At high speeds, radial tires also heat up more slowly, which means that they have less damage to the tread.
In 1909, the sidewall of a tire was 13 percent higher than the tread width. Since then, this ratio has been completely turned upside down: modern tires are on average four times as wide as they are high. The wider contact patch improves traction and gives the vehicle more grip.
Until 1904, tires were produced exclusively with a smooth surface. This year, Continental was the first company to develop a tread pattern that significantly improved the performance of tires, such as their power transmission, grip, braking distances and cornering stability.
A tire consists of up to 100 different raw materials. Some take a larger share, others a smaller one. But regardless of the quantity, each material has special properties and therefore has a decisive influence on tire desig
Rubber is the material with the largest proportion in a tire. But not all rubber is the same. The natural rubber derived from plants is essential for the excellent functionality of tires. Its special properties include high shock resistance and durability. In addition to it, countless variants of synthetic rubber can be produced in the laboratory. The first tire made with synthetic rubber was built in 1911. Today, synthetic rubber is used in almost every tire, as it can be tailored to all requirements and ideally complements the natural product.
In an effort to make our tires stronger and more durable, our developers experimented with different types of reinforcing fillers. In 1926 we used carbon black for the first time. The easier it was to bond the filler to the rubber, the firmer the tires became. The material helped to improve the rigidity, hardness and grip of the tire on the road and, most importantly, its abrasion resistance.
Today, about 100 different types of carbon black are known, which differ in the size and shape of their main components and surfaces. About 40 of these varieties are used in tire manufacturing. We can now use recycled carbon black from our partnership with Pyrum Innovations
In addition to industrial carbon black, silica is also an important filler. Silica helps to significantly optimize tire properties such as grip, rolling resistance and mileage.
In 1993/1994, Continental carried out its first trials with silica. This made Continental one of the pioneers in the market. The tests were successful: In 1995, the ContiEcoContact CP was introduced, which included silica in its rubber compound as standard. Continental was the first manufacturer to use silica in winter tire compounds (1996 / ContiWinterContact TS 770). Silica has since become more and more established as a carbon black substitute among premium tire manufacturers. Today, there are no longer any premium passenger car tires that are manufactured without silica.