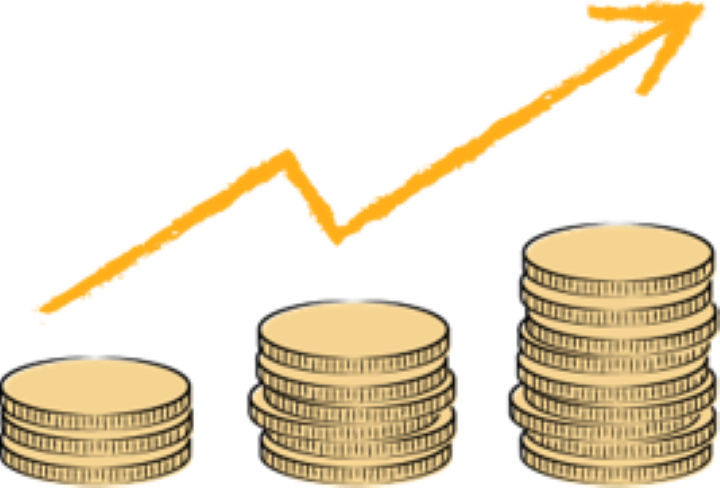
Several factors can contribute to downtime for regional and local fleets:
Downtime can have a significant financial impact on regional and local trucking companies, including:
By implementing proactive strategies, regional and local trucking companies can significantly increase fleet efficiency and reduce costs.
By prioritizing preventative maintenance, investing in driver training, optimizing routes, and leveraging technology, regional and local trucking companies can significantly improve fleet uptime. Partnering with a reliable tire provider like Continental Truck Tires can provide the resources and expertise needed to keep your fleet running smoothly and deliver on your promises. Continental's commitment to helping fleets achieve the Lowest Overall Driving Cost goes beyond just tires, encompassing a holistic approach to fleet management.